
Explosion-proof industrial vacuum cleaners: the ultimate guide
Industrial vacuum systems for use in Hazardous Locations or Ordinary Locations with Combustible Dust
Many accidents have happened in the past, but after the Imperial sugar disaster in 2008, where 14 people died as a result of an explosion caused by sugar dust, world organizations were sensitized to the creation of new standards and policies preventing such disasters.
Starting from that event, OSHA (Occupational Health and Safety Administration) and the NFPA (National Fire Protection Association) started to develop monitoring programs for North America in order to assure themaximum safety level possible in industrial manufacturing processes.
Industrial vacuum systems were unavoidably involved in these new policies as they represent both:
- Possible source of ignition, if not properly equipped
- The best solution and recommended cleaning method for suction of hazardous dusts

Which policies were created to protect facilities from hazardous dust risks?
Environments classification – NFPA 70 / NEC
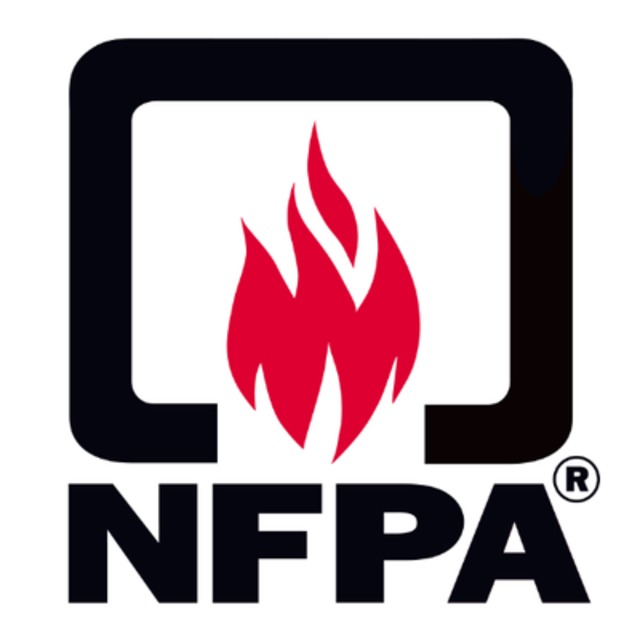
NFPA set a classification of dangerous environments based on the type of risk and on its frequency in presence of combustible dust.
Other 2 regulations (NFPA 654 - Standard for the Prevention of Fire and Dust Explosions from the Manufacturing, Processing, and Handling of Combustible Particulate Solids and NFPA 484 – Standard for combustible metals) both define combustible dust as “any fine solid material that is 420 microns or smaller in diameter and present a fire or explosion hazard when dispersed and ignited in air”.
This is why even non classified environments must comply to the housekeeping and cleaning regulations: not only the generally recognized hazardous industries (as pharmaceutical and petrochemical industries) are vulnerable to hazard dust explosions, but also agriculuture, food industries (such as feed, flour, candies, spice, coffee), tobacco, grain, fertilizer, plastics, wood, paper industries, pulp, textiles, furniture, tire and rubber manufacturers, dyes, coal and metal processing (such as aluminium, iron and zinc).
Standard on the fundamentals of combustible dust – NFPA 652
The NFPA created its own regulation in order to set standards to deal with combustible dust in industrial environments, the NFPA 652.The NFPA 652 applies to all facilities that manufacture, blend, package, repackage, convey, or handle combustible dust or particulate solids that may become dust (even in presence of not classified environments) and states that each plant must have:
- On file a copy of their dust type testing
- A complete Dust Hazard Analysis in order to prevent dust related hazards.
- Documented housekeeping procedure listing these methods of cleaning in order:
- Properly equipped industrial vacuums
- Brooms, mops
- Blowguns (only where ignition sources are not present)
National Emphasis Program – OSHA
OSHA gives a guidance that all industries must follow called NEP (National Emphasis Program), which lists recommended housekeeping and maintenance procedures.Even if the NEP is not an approved regulation, this does not mean that it can considered without penalty. There are some standards that can be used for regular citations.
The recommended procedures include:
- Detailed working environment cleaning program, defining the materials which may be combustible, the processes to avoid explosions, hidden areas in the facilities that have to be checked regularly, source of ignition
- Use of industrial vacuum systems as the best and safest choice for cleaning
- Only use certified equipment for the scope, both as outlined by the environment (HazLoc) or for safely picking up the dust type (Combustible / Non-combustible) as identified in your Dust testing and DHA.
Certified or compliant to NFPA and OSHA standards?
It is not possible to certify any equipment or vacuum cleaner by NFPA or OSHA standards, because they are not certification authorities. Only an NRTL (Nationally Recognized Testing Laboratory) may certify equipment for use in Hazardous Locations. The NFPA and OSHA provide specifications that vacuum cleaners (and general equipment) must have when collecting combustible dust. An industrial vacuum cleaner can only be compliant to NFPA and OSHA standards, and it happens when it features:- Complete earth grounding
- Conductive accessories, correctly bonded to be safe
- The fan must be well protected from the dust particles
- Antistatic filters
- There is no paper filter
- Specific Ohm testing for each part of the machine must meet the criteria outlined in the standards for each dust type or environment.
Explosion proof industrial vacuum certification
Only electrical equipment can be certified and the only authorities able to do that are the NRTLs (Nationally Recognized Testing Laboratory). They are the only bodies that can provide certifications for electric equipment in the United States.Note: Pneumatic equipment cannot be certified by an NRLTs, because there is no certification for pneumatic equipment in the United States.
How to choose a certified explosion proof industrial vacuum system?
Each class and division requires different specifications and NRTL certifications (depending on the frequency for the hazard and on the type of combustible dust). A suitable industrial vacuum system must be built in order to prevent the formation of sources of ignition. The vacuum system must therefore prevent the formation of static electricity, percussion arcing, electric arcing and the overheating of the motors.
The main features of a compliant industrial vacuum systems are:
- Antistatic filter with M class of filtration
- Earth grounding
- No available source of ignition
- Motor protected from external dust contamination
- Antistatic castors
- Stainless steel collection bin
- Low sparking inlet and internal deflector
Delfin Explosion proof industrial vacuum systems
Delfin expertise helped to develop a range of explosion-proof certified vacuum cleaners. Many other industrial vacuum systems are compliant to NFPA regulations.NRTL Certified vacuum systems
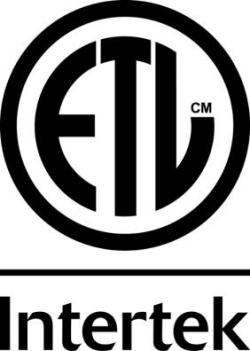
Delfin industrial explosion-proof vacuum cleaners are NRTL certified (ETL Intertek listed) and are manufactured in order to avoid any risk of ignition in a potentially explosive environment.
The certifications for UL and CSA available are:
For ordinary locations (all the vacuum cleaners is covered by this assessment):
For hazardous locations:
UL 1203 and CSA C22.2 No. 25 and No. 30 for explosion proof and dust ignition proof vacuum cleaners
ISA 12.12.01-2016 and CSA C22.2 No. 213-16
Each vacuum system is designed to comply with highest standards, ensuring safety, quality and reliability. If you have to collect highly explosive dusts or need to use vacuum system in potentially explosive atmospheres, our full range of NRTL-certified vacuum systems and accessories guarantees all the security and reliability you need.
NFPA Compliant vacuum systems
Delfin offers also a wide range of industrial vacuum systems which are NFPA compliant, from the most compact, transportable and resistant machine to the large fixed one dedicated to centralized vacuum cleaning. Thanks to the variety of available options we are able to satisfy almost any type of request:- Producer certified motor with power ranging from 2 HP to 25 HP
- Antistatic M Class filter as a standard
- H Class filter as a standard in some vacuum cleaners
- Stainless steel AISI 304 or 316 construction available
- Certified components
Contact us to discover our explosion proof solutions!

Compact single-phase vacuum cleaners

Heavy-duty single-phase industrial vacuum cleaners
Delfin's heavy duty single-phase industrial vacuum cleaner features the classic yellow and blue and can be equipped with two or three by-pass motors Ametek Lamb.

Three-phase industrial vacuum cleaners
Solid, capable and powerful, the three-phase industrial vacuum cleaner is equipped with turbines ranging from 2.2 to 5.5 kw, is characterized by large filter surface and containers between 50 and 100 lt. This vacuum cleaner, which in Delfin's range is represented by 4 models of the DG EXP line, can also be used as a suction unit in small centralized systems, in combination or not with filtering preseparators or hoppers.
The real strength of this type of industrial vacuum cleaner is its reliability. In fact Delfin equips its industrial vacs only with Italian, German or American side channel blowers, which ensure outstanding performance, even in continuous and very heavy applications. The side channel blowers used, moreover, are suitable to work continuously and can work without problems even 24 hours 24 (in these cases it is recommended to adopt a safety valve that protects the turbine from overheating, allowing it to virtually work to infinity) .

Heavy duty three-phase industrial vacuum cleaners
The high performance industrial vacuum cleaners free themselves from the simple concept of "vacuum cleaner" to become machines for material handling and pneumatic conveying. With their enormous power (turbines up to 25 kW) in fact they can carry powders and solids with many features for tens or hundreds of meters, and then discharge them via hoppers or separators. For this very reason Delfin's Heavy duty three-phase industrial vacuum cleaners , which can be found in the DG HD line, are very often used as a central vacuum unit in centralized vacuum systems. Given the great power these are almost always combined with systems of pre separation and hoppers which are, in turn, designed and constructed based on the needs of the end user.

High vacuum units
High vacuum units have incredible high depression in order to collect heavy dust or granular solids dispersed during the manufacturing process, typically in cement plants, steel mills, mining and other heavy industries. The use of these suction units increases the efficiency of the production cycle, allows the saving of considerable resources in terms of both manual labor and in terms of production downtime while it increases the hygiene in the work environment. Furthermore the collection of these materials generates immediate savings because these can be directly replaced in the production process. The industrial high vacuum units are in fact designed for the recovery of large quantities of heavy materials, also of large size.
The incredible effectiveness of these tools allows a rapid return on investment derived from significant savings in terms of manpower and time. Delfin's high vacuum are built with a sturdy steel structure, which protects, inside it, a vacuum pump and a mechanical system extremely simple and at the same time effective. This com
This combination guarantees the absolute reliability of these incredible industrial vacuum systems.

Industrial air powered vacuum cleaners
Delfin's compressed air operated vacuums generate suction through one or more Venturi ejectors. These ejectors have no moving electromechanical components therefore are extremely reliable and durable. Delfin recommends this type of vacuum cleaners especially for shipyards and applications on board of ships or oil platforms, where the air supply is preferred to electricity. Air operated vacuums guarantee excellent performances and the ability to work continuously, even 24 hours 24.

Vacuums for fixed extraction on machines (OEM)
The industries manufacturing production machinery, from the machines for the packaging to those for cutting aluminum, very often have the need to recover small quantities of dust and / or production waste (also scraps), directly to the source and continuously.
These companies, known as Original Equipment Manufacturers, therefore require compact and modular suction units, which also have to be highly customizable depending on the performance required by the specific application. Delfin's units of the DirectX line are the preferred choice of multiple leading manufacturers of industrial machinery, ranging from bottling machines to CNCs.
Delfin has earned this preference thanks to a very high level of flexibility and adaptability to customer requests, each time coming to the creation of the best possible suction unit.

Vacuums for continuous recovery of waste and scrap
The vacuum units for continuous recovery of scraps are distinguished from most industrial vacuums for their cylindrical shape. These machines are in fact constructed in order to have a large internal volume of collection, as they are mainly used for the continuous recovery of scraps and waste of production on packaging lines or textile machinery. In fact on these machines, scraps are often strips of material, long and light, but very voluminous.
This suction unit is composed of a side channel blower placed on the bottom of the cylinder, above it there is a grid of protection, while the remaining part of the cylinder is covered by a filtering bag, made of filtering material.This bag is fixed thanks to the plug located in the apical part. The bag, when filled with waste and scraps can be easily removed, emptied and replaced.
These vacuum cleaners therefore guarantee the operation of the machines on which they are applied without jams (due to scraps) and minimizing downtime for immediate savings.

Dust, fumes, mist extractors

Centralized vacuum systems
Centralized vacuum systems allows the cleaning, removing and transporting of dust, powders or materials from one area to another, through a series of fixed pipes (normally fixed to the wall), accumulating and discharging them in a chosen point.
Request information