What is ATEX: the ultimate guide
How to choose the right vacuum cleaner according to ATEX regulations?
Today's regulatory landscape, made up of both national and European regulations, does not simplify the work of Health & Safety Managers and all those people that are concerned with ensuring the safety of their companies.
The aim of this guide is to shed light and ease the understanding of the ATEX Directive with regard to the ATEX certified industrial vacuum cleaners.
We will analyze:
- What is ATEX and where is it applied?
- The areas of risk or the probability of risk
- ATEX vacuum cleaner: what features should it have?
- Delfin's ATEX industrial vacuum cleaners
What is ATEX and where does it apply?
What is the meaning of ATEX? ATEX is the contraction of French words ATmosphères EXplosibles and is the code that includes two European Union directives concerning safety issues. The first, Directive 94/9 / CE, regulates the use of equipment and machinery in areas at risk of explosion. It is addressed to equipment manufacturers, in particular, regulating the technical safety features they have to comply with in the different areas of risk. The second part of the ATEX directives are based on the 2014/34 / CE directive, which concerns the protection of the health and safety of workers in potentially explosive atmospheres. This is, therefore, aimed at companies that may operate in dangerous areas.
Where does ATEX regulations apply?
The directive, which came into force in 1996 and became mandatory in 2003 for all the states of the Union, calls for the ATEX certification of all machines sold in the EU itself, regardless of the place of production and the regulations in force in it, if installed in areas at risk of explosion. In Italy it has acquired the force of law by the Decree of 23/03/1998 n. 126.
ATEX explained: where can an ATEX risk zone be created?
Although it is widely believed that the danger of explosion is only a worry of the petrochemical industry, refineries and pharmaceutical industries, in reality the issue concerns many other sectors and companies.
In fact, under certain conditions, common materials such as flour powder, light metals, wood, leather, carbon fiber, seeds, sugar, paper, cardboard, waste fuels and organic compounds can cause explosions.
In the last decade there have been several tragedies caused by explosions in both national and international companies. Just think of the explosion of grain storage silos, back in 2007, in Molino Cordero di Fossano (Piedmont, Italy), in which five people lost their lives, or the disaster of 2008 at the Imperial Sugar refinery in Georgia, USA, where the victims count reached 14 dead and 42 wounded people.
In both these cases the explosions have occurred due to the wrong handling of powders and a poor cleaning of installations which, in the long run, have given the possibility to an explosive atmosphere to arise and explode.
This is the ATEX logo

ATEX ratings explained: The areas and probability of risk
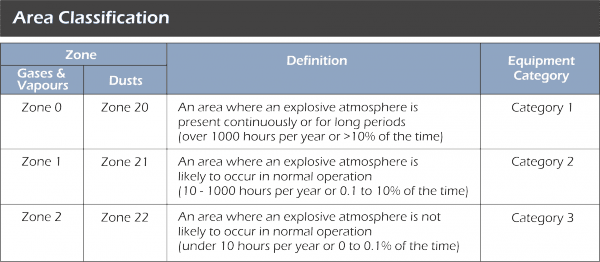
Risk is defined and calculated as the ratio between the working hours in a year and the hours in which it is probable the presence of an explosive atmosphere, which is why we talk about probabilities.
That is why risk zones are divided as follows:
- DUST HAZARD ZONE 20: A place in which an explosive atmosphere, in the form of a cloud of combustible dust in the air, is present continuously, for long periods of time or frequently (eg. Hoppers, silos, cyclones and filters - powders transport systems, internal mixers, grinders, dryers, bagging equipment, etc..).
- DUST HAZARD ZONE 21: A place in which an explosive atmosphere is likely to be present in the form of a cloud of combustible dust in the air during normal operation.
- DUST HAZARD ZONE 22: A place in which an explosive atmosphere, in the form of a cloud of combustible dust in the air, could occur, but would persist for a short period of time.
- GAS HAZARD ZONE 0: where an explosive atmosphere is continuously present, for long periods of time, due to presence of gas.
- GAS HAZARD ZONE 1: where an explosive atmosphere is likely to be present during normal operations, due to presence of gas.
- GAS HAZARD ZONE 2: A place where it is not possible to have an explosive atmosphere due to the presence of gas during normal operations or, if this occurs, it is possible for it to be present with a low frequency and for a short term.
ATEX Vacuum cleaner: what features should it have?
What are the characteristics that must therefore be implemented on an ATEX vacuum cleaner in order for it to be considered safe to use in hazardous areas?
An ATEX vacuum cleaner must be built in order to prevent the formation of sources of ignition. The vacuum cleaner must then prevent the formation of static electricity (via grounding, antistatic filters and accessories), the overheating of motors (through specific certified engines) and other devices.
All the industrial vacuum cleaners of the wide Delfin ATEX range meet and exceed the safety requirements imposed by the regulations, being always equipped with ATEX certified motors (feature only required by norm only for Zone 21 equipments).
Delfin's ATEX Vacuum Cleaners and ATEX centralized vacuum systems
Delfin has been building ATEX vacuum cleaners and ATEX central vacuum systems for over 25 years, through a controlled manufacturing process, in order to provide the safest vacuum cleaners in the industry.
With over 20 certified models (not mentioning the 4 air powered ATEX certified industrial cleaners of the AIREX range) Delfin can provide the right solution, not only in terms of safety, but also performance and sizing compared to the specific applications with ATEX approval.
All of Delfin's ATEX vacuum cleaners have the following features:
- Antistatic filters certified in Class M as standard (1 Micron efficiency)
- Antistatic filters certified in Class M, plus Class H filters (HEPA or absolute) as standard for ATEX vacuum cleaners in Zone 21.
- Totally built in AISI 304 or 316 stainless steel (as standard for the AIREX range)
- ATEX certified electrical components
- Safety cap for the safe cleaning of filters, avoiding any dispersion of dust in the environment
- Integrated filter cleaning systems, automatic or manual, depending on the model
In addition to mobile ATEX vacuum cleaners, Delfin has also been providing ATEX centralized vacuum systems certified for industries in the food sector (mills, factories, bakeries, etc..) and both for the chemical and pharmaceutical fields (central vacuum cleaning systems have been implemented in industries throughout the world).
Watch now the Video Case History of the central vacuum system implemented in several facilities of wheat flour processing giant SEDAMYL:
In the end, should you need an ATEX vacuum cleaner for the cleaning of labs or production lines, rather than designing a centralized vacuum system for an entire factory.
Our technicians will help you to choose the correct ATEX certified vacuum cleaner for your business.